If you have a farm, you're bound to have plenty of electric motors. You likely do not have the time to hire qualified personnel to regularly check your electric motors, so we are hoping to help you out with a little information to use yourself.
Check out our video with motor expert Hal to learn about some general motor maintenance tips, and read on for more details on electric motor maintenance.
Electrical Equipment
First, let's go over some electrical components and tools needed to perform maintenance checks.
- Flashlight
- Volt Meter
- Infrared Camera (optional but suggested)
- Screw Drivers
- Grease & Grease Gun
- Screw Drivers
- Compressed Air
Preventive Motor Maintenance
Preventive maintenance is the first type of inspection you should use regularly for electric motor health. Almost all electrical equipment can benefit from preventive maintenance as the purpose is to prevent operating problems and electrical dilemmas before they start to get serious. Preventive maintenance should be a regular, scheduled part of your farm's operation.
This form of electric motor maintenance includes making sure all equipment is running smoothly and documenting any current or potential problems. Documenting your periodic inspections can be overlooked or underrated, but it can save your motor's life by making sure your motor continuously can avoid failure.
Think of preventive maintenance like going to the dentist twice a year- you aren't necessarily going to the dentist because there is a problem, but instead to check in on things and make sure there aren't any warning signs of a larger issue.
This type of maintenance has several benefits. Performing preventive maintenance is a very efficient way to increase your equipment's life span. Periodic inspections prevent unplanned downtime of your electric motors, and stops major issues before motor failure occurs.
Preventive maintenance on a farm should never be considered a waste of time. Sure, sometimes this maintenance occurs and no problems are found, but it prevents unplanned downtime. This is vital to the proper operations of any farm, especially if you are keeping livestock.
Motor Ventilation
An ounce of prevention is worth a pound of cure and motor ventilation is worth at least 16 ounces. If you're a poultry farmer, you know how dang dusty a poultry house is and always will be. Making sure that your motor housings are ventilated and not suffocating in dust is so important.
During inspection, always have compressed air or a blower to remove dust and debris. Once you have a cleaned motor, inspection of the air flow and temperatures is key.
Motors need to be warmer than the air around them so that you eliminate internal humidity and condensation. While it is rare on small motors, you may have a drain plug to pull to remove water collection. Again, blowing around the motor to remove moisture is a strong suggestion.
Visual Inspections for Preventive Electric Motor Maintenance
It's important to visually inspect all aspects of the motor. Look for a burn marks from overheating, and check with the motor running so you can attempt to detect burning odors. Inspect the bearings to see if there is any vibration or noise, and grease all bearings. With a small flashlight you should review and examine the switches and fuses and be sure to tighten loose connections you identify. With the motor off, use light compressed air to clean the components. Performing maintenance checks yourself is a great way to get a status update on your machinery.
Check Bearings and Bearing Life
Besides electrical malfunctions, bearings are the single biggest issue on an electric motor. Bearings can be very difficult to inspect and require some thought and deeper digging.
Motors have a main bearing in the front of the housing and in the back of the housing. These likely do not require regular grease applications or lubricant, as most modern motors are considered "maintenance free." This is a misleading term and it is very possible that the rest of your components will outlast the bearings.
Look for the normal wear signs on the bearings such as wobbling and side play, shifting, erratic motor RPMs and suspicious noises during rotation.
The challenge with bearing repair is time and cost. Often replacing bearings is an easy task that would not require much time if your motor is accessible and if you enjoy shop time. Most young farmers today have a "throw in the gutter and go buy anutter" mentality. If you have invested in a quality motor, repairing and replacing the bearings is not difficult. Just take it from Mr. Pete!
Predictive Maintenance
Predictive maintenance should tell you the right kind of maintenance that needs to be carried out and at what time. Predictive maintenance is different from preventive because instead of being regularly scheduled, it is conducted in response to real-time data collected by your machinery in order to address small issues and prevent unexpected production stops.
Predictive maintenance can be compared to going to the doctor's office when you are starting to feel sick but are not in an emergency situation.
Benefits of predictive maintenance include identification of issues before electrical products face serious damage and locating potential problems. It also improves inventory efficiency, as it can show you which parts to replace before they fail but not while they are still usable.
Infrared Images for Predictive Maintenance Success
There are many, many uses for infrared cameras and technologies to be used on a poultry farm. Infrared thermography (IRT), thermal video and infrared imaging are all techniques that use infrared radiation from an object to produce an image of it using a thermal camera. This can be very helpful when evaluating or inspecting an electrical motor. These images will show the motor temperature and heat patterns.
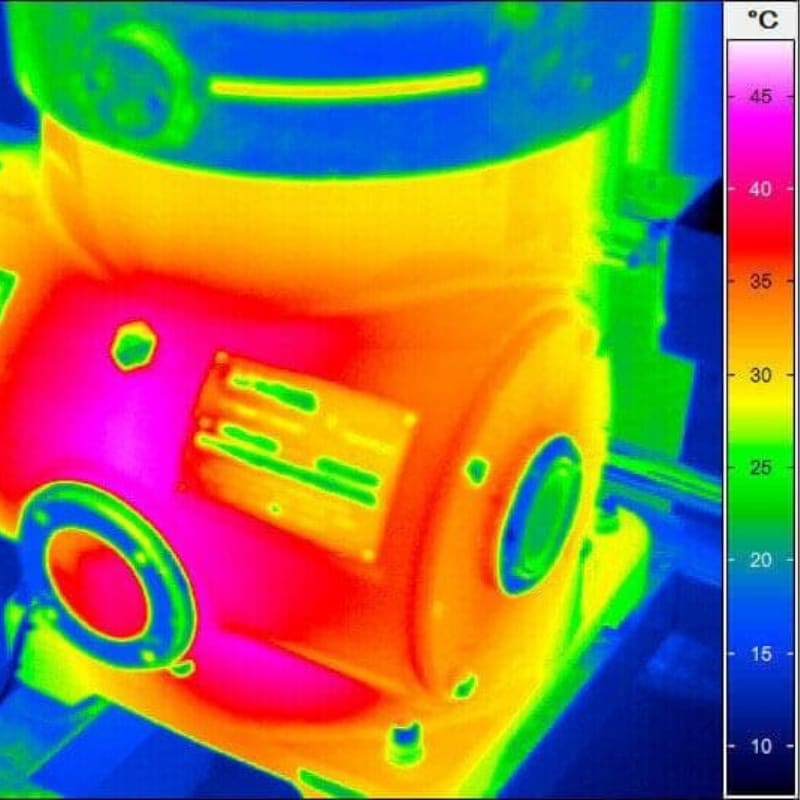
Armed with the knowledge of heat patterns and motor temperature, you'll be able to spot trouble areas like poor air flow, insulation flaws or motor stator deterioration. An infrared camera can also quickly find hot spots which can be an indication of insulation damage or unbalanced windings. IRT tech is able to see not only the surface temperature but also up through the layers to give a complete picture of what's happening under the surface.
This technology helps you get a better look at electric motors more efficiently. IRT tech will allow you to see your motor's heat signatures without using intrusive tools like contact thermometers that might otherwise hinder workflow. When choosing infrared imaging for your farm, make sure it provides low-noise video images at distances ranging up to 100 feet. This is handy when trying to pinpoint problem areas on equipment with multiple small components and details.
Vibration Test
Motors rotate very fast. At some point, a motor is likely to start vibrating when something comes out of balance or the bearings need repair.
Step one is to identify if any out of place vibration is occurring. Do this by listening to the motor and placing your hands on the motor for detection. There will be two parts that you want to test- the motor housing and wherever the shaft is attached. By making a distinct inspection of the two sides you can isolate between the two parameters.
All too often, a simple vibration test will detect a pulley that is out of alignment or taking wear from a belt. A broken pulley is unfortunate and causes downtime. A simple vibration test on a regular basis can help you avoid failure.
Vibration Test Key Points
- Are all the nuts and bolts tight?
- Are the mounting bolts flush? Are any shims needed to create even pressure on the plate?
- Are the pulleys or external gears aligned properly?
- Is anything vibrating excessively? If so is it due to the internal bearings, alignments or could simple rubber gaskets solve the issue?
- Are any parts of the motor or shaft loose?
- How are the fan blades and the fan cover?
Insulation Resistance Test
An insulation resistance test can show how much electricity is getting through to the other side of the wiring insulation. The test determines how effective the insulation is in resisting the flow of electrical current. If you have worn insulation you could cause an arc or a short that would be indicated.
A goal of both preventive and predictive maintenance is to prevent the next level of maintenance- reactive.
Reactive Maintenance
Reactive maintenance, or breakdown maintenance, occurs when critical repairs are necessary. The purpose of this type of electric motor maintenance is to repair or replace the motor in the case of failure. Reactive motor maintenance is typically unplanned and, as the name suggests, occurs as a reaction to a failure. This should be your last resort when maintaining electric motors, as it usually more expensive and requires more downtime. However, sometimes you gotta do what you gotta do. Reactive maintenance is better than shutting down your farm!
When an electric motor fails, you'll need to examine it carefully and identify what went wrong. All equipment related to the area of failure will also need to be checked in order to prevent motors from failing in similar ways in the future.
Perform a Motor Winding Test
A motor winding test simply detects if the motor is going bad. The idea is to test the connectivity of the wires that create the loop of the current to see if they are getting worn. This detects problems before the motor stops completely. Learn more by watching this helpful video from Astral Pool in Australia:
- Unplug the motor.
- Disconnect the capacitor or starter switch. If your motor is hard wired then shut it off at the circuit breakers.
- Set your multimeter to test the Ohms or the resistance on the circuits.
You want to look for a reading of between .3 and 2 ohms.
A reading of 0 means that there might be a problem. When the wires short to ground, it usually leads to a break in the wire. If you get a reading of 0, double-check and test again.
If the reading is more than 2, you probably have an open winding. An open winding indicates that your motor's wire is broken.
Conclusion
Overall, it's best to check motor operation regularly. Electric motors are critical to the success of your farm, so giving them regular service can make all the difference in saving you time and money.
We hope this blog helps you out! If you have any questions or ideas for future topics, please reach out to allen@southlandorganics.com. Check out our Poultry Biosecurity blog and YouTube page for more tips on how to make your farm business successful.